- Ruhr-Universität Bochum
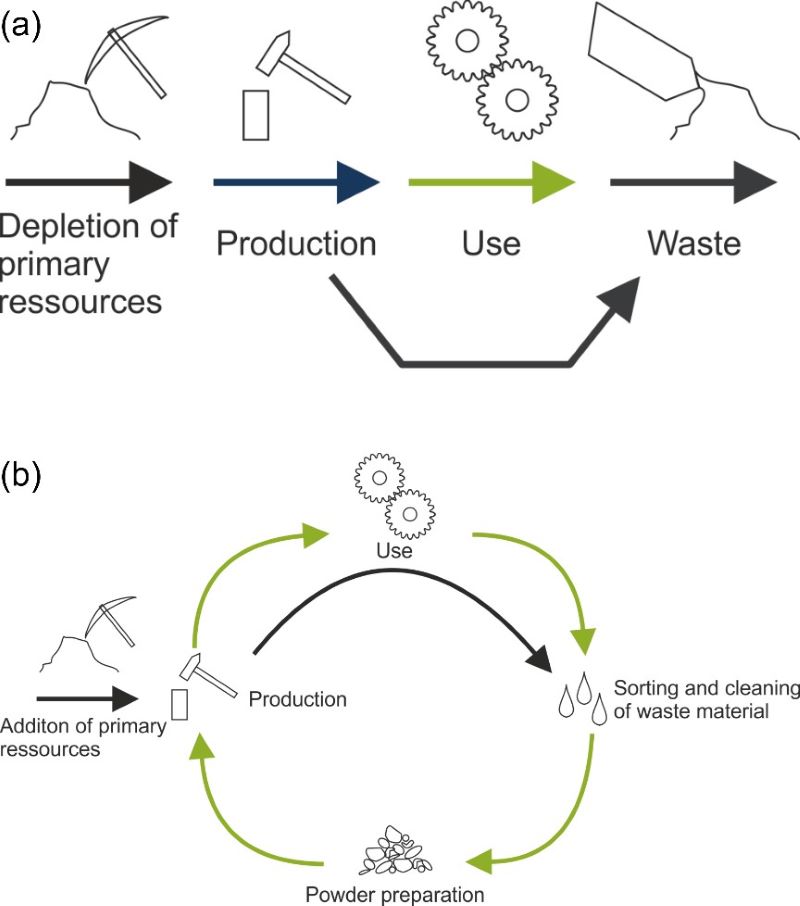
Circular economy of critical metals
The development of a circular economy of critical metals is an important requirement for a sustainable future. Advances in electro mobility and the transition to renewable energies increase the demand for critical metals. These metals include rare earth elements such as Neodymium and Terbium which are needed for the construction of highly efficient electric engines and generators. Also, rare and expensive alloying elements like Cobalt, Molybdenum, and Tungsten that are used in high performance alloys can be considered critical. By now, thousand of tons of these materials are dumped while new components are produced from mined primary raw materials. Besides, the depletion of primary raw materials is coupled with high demands of energy and environmental destructions. Furthermore, the locations and the limitation of the reservoirs of the critical raw materials lead to geostrategic dependencies and high economic risks.
To overcome this linear type of economy and to establish new circular economy systems, ways to re- or upcycle critical metals are investigated. Today, available recycling strategies are not competitive from an economic point of view. For this reason, there is a need for further investigating and developing recycling methods for critical metals. Our investigations within the research project “GENESIS”, funded by the German Ministry of Economics and Climate Protection (Bundesministerium für Wirtschaft und Klimaschutz, BMWK), focus on a powder metallurgical approach to recover critical metals. Scrapped products such as the rare earth element containing components of electric engines or generators can be mechanically crushed to powders that can be used again as secondary raw materials for the production of new components. Other types of scrap are grinding sludge or chips from the subtractive machining of metallic high-performance components which can contain large amounts of critical alloying elements. To recover scrap materials for powder metallurgical processes in particular, efficient methods for sorting, cleaning and crushing to powder material have to be found. The powder metallurgical route for re- and upcycling of the otherwise dumped materials offers a wide range of energy and material efficient manufacturing methods to produce new components from the waste materials. These methods include near net shape sintering and additive manufacturing techniques.
Field assisted short time sintering processes utilizing impulses of electric current (FAST-SPS) are adapted for the recycling materials and combined with integrated hot forming (FLASH-SPS) to set up desired microstructures and therefore produce high performance neodymium-based magnets at a low energy consumption. Furthermore, the production of high strength steel parts from waste material from subtractive machining by hot isostatic pressing (HIP) is investigated. Thereby, state of the art hot isostatic presses with integrated rapid gas quenching are used to combine the consolidation of the recycling powder with the heat treatments that are required to set up the mechanical properties of high strength steels.
The investigated and further developed powder metallurgical manufacturing techniques can reduce energy intensive production steps like multiple forming, machining and heat treatment procedures in the processing of critical materials. In addition, the goal is to recover the vast amounts of available and already dumped critical metals and keep them in a circular economy to substitute the use of primary resources. This is an important step to a cleaner production of the highly demanded components of a more sustainable future.