- Ruhr-Universität Bochum
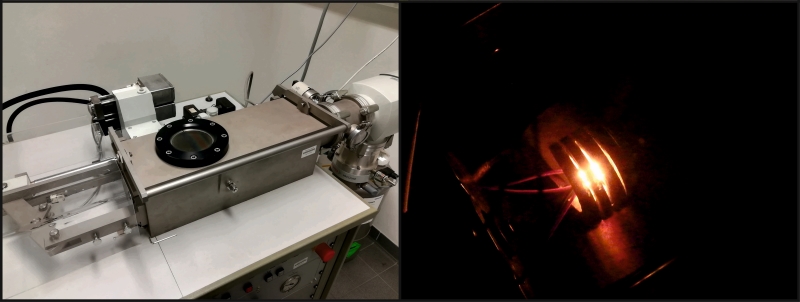
Energy-efficient heat treatment of high-alloy steels
The metal processing of high-performance tool steels usually consists of a multitude of consecutive manufacturing steps. Besides the forming and machining processes, the heat treatment is one of the most important and energy-intensive steps in the manufacturing process. This is because the properties of the material, and thus those of the manufactured tool, are determined by the microstructure present. The microstructure, in turn, is primarily determined by the chemical composition and the complete processing history. In the case of high-alloy tool steels, the microstructures are typically complex multi-phase systems.
Conventional industrial heat treatment of high-alloy tool steels consists of austenitizing at temperatures above 1000 °C in a natural gas-fired hardening furnace, followed by quenching to room temperature. This is currently followed by a multi-stage tempering at temperatures in the range of 500°C, typically in an electrically heated furnace. This energy-intensive heat treatment alone can be used to estimate the high energy demand in the production of high-performance tools. The exact temperatures and holding times of the heat treatment of a tool are determined and optimized using a complex experimental test matrix. Subsequently, the heat treatment determined in this way is applied in production for the tool steel and the tool used. However, due to the production process, e.g. recycling of material, there are slight differences in the chemical composition of the starting material, which leads to deviating mechanical properties. In the worst case, this can lead to rejects due to the insufficient mechanical properties of the tools.
Due to the challenges described above, we have developed a heat treatment simulation model using the ledeburitic cold work tool steel X153CrMoV12 (1.2379) as a model alloy. The model considers the chemical composition as well as the microstructure of the starting material (and thus the complete manufacturing route) and calculates the microstructure after heat treatment as a function of the hardening temperature and holding time. The schematic sequence of the simulation model is shown in Figure 1. The model was validated by experimental execution of the heat treatments using a quenching dilatometer (Figure 2). Two different hardening temperatures with six varying holding times each were successfully tested. For a given time-temperature history of the heat treatment, the developed simulation model can compute the carbide dissolution, the concentration of alloying elements in the matrix, and the martensite start temperature. From these data, mechanical properties can be derived.
With the model, we now can simulate local differences between component edge and component core. On the other hand, we can vary the hardening temperature and dwell times to reduce the total heat treatment time while maintaining the same properties and thus increasing efficiency. Furthermore, it is possible to adapt the heat treatment to the changing chemical composition of the starting material to guarantee the required mechanical properties and thus the process stability in production. With the help of the simulation model, an alternative heat treatment was developed for a conventional application. The new heat treatment comes along with a lower hardening temperature and requires significantly lower holding times than the conventional process. In addition, this low-temperature heat treatment requires only one stress-relieving tempering step at temperatures of approx. 200 °C, compared to the current three tempering steps at temperatures of approx. 500 °C. In experimental laboratory tests, this developed heat treatment achieves identical mechanical properties, or even surpasses those of conventional heat treatment in other areas. If the heat treatment developed by the simulation and investigated on a laboratory scale can also be used in industrial production, this will result in a significant reduction in the energy required for production. This would lead to a more sustainable production and thus to an optimized overall process chain while maintaining the same product quality.