- Ruhr-Universität Bochum
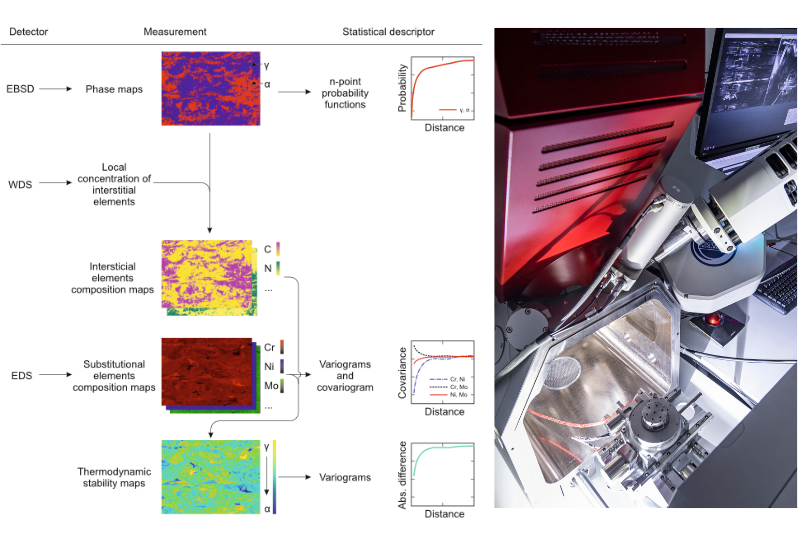
In-situ alloying in additive manufacturing
Additive manufacturing, in which a component is built layer by layer directly from a 3D CAD model, enables the rapid and resource-efficient production of highly customized and complex components. One manufacturing route used in particular for the processing of metals is the Laser Powder Bed Fusion (PBF-LB/M) process, in which metallic powders are locally melted by a focused high-energy laser beam, causing metallurgical fusion between the multiple layers of molten powder. The focused laser energy input leads to high temperature gradients and results in high solidification and cooling rates of the melt. These thermal conditions currently limit the materials that can be processed using PBF-LB/M, slowing the progress of additive manufacturing towards large industrial applications.
Because of this limitation, we are working on new materials that are PBF-LB/M-processable and also have improved properties, such as higher strength or corrosion resistance, compared to currently-available materials. However, alloy development is generally expensive due to the starting powdered material, which is produced using cost-intensive and time-consuming gas atomization. As a result, in-situ alloying (ISA) has recently gained popularity, where at least two starting powders (elemental or alloyed powders) are mixed prior to PBF-LB/M processing and then metallurgically fused during manufacturing. During PBF-LB/M, chemical inhomogeneities occur depending on the degree of difference in the chemical composition of the starting powders and the parameters used in the process. These inhomogeneities influence the local phase formation and thus the overall microstructure formation of the additively manufactured component, which, in turn, influences the emerging properties. The characterization of these inhomogeneous microstructures is essential for understanding the reigning process-structure-property correlations. To that end, we use a combination of different analytical techniques. Electron Backscatter Diffraction (EBSD) is used for local phase analysis and phase fraction quantification, and is accompanied by quantitative elemental mapping of the substituent elements using Energy dispersive X-ray spectrometry (EDS), allowing the phase information obtained from EBSD to be directly related to the local chemical composition. To quantify the phase-dependent chemical concentration of the interstitially dissolved elements such as C and N, Wavelength Dispersive X-Ray Spectrometry (WDS) measurements are additionally performed. We use the aggregated data from these investigations to quantify the degree of inhomogeneity, e.g. as a function of the alloy system or the energy introduced in the process, and also to establish a link between the phase formation and the local chemical composition. In this context, as indicated in the flowchart below, we employ thermodynamic calculations to determine the local phase stability as a function of the local chemical composition, giving rise to the so-called stability maps. From this, transformation tendencies can be deduced, which is particularly important for mechanical behavior.
The analytical techniques employed provide a wealth of spatial information, certainly enough to fully describe chemical and phase stability inhomogeneities. However, to go beyond their mere qualitative examination and comparison, we need description methods that condense the data into useful, physically meaningful descriptors. Drawing from spatial statistics, we employ statistical tools that can simultaneously characterize inhomogeneities thoroughly and provide deep insights into their physical context. These are variograms, covariograms and n-point probability functions, point-symmetric descriptors that present structural spatial variations with high information density. A good place to start explaining them is the variogram: it shows the difference in property values between all pairs of points separated by a given distance in a given direction. So, as shown in the flowchart, we use it to describe and understand the spatial variation of alloying element concentrations. Covariograms are similar, but display the covariance of the distribution of two variables. Fittingly, they can be deployed to characterize the segregation behavior of substitutional elements. Finally, n-point probability functions detail the extent and distribution of regions in a map. These regions are usually the phase domains. Further, the resulting stability maps can be subjected to the variogram analysis described above. The information collected and condensed by these descriptors casts light on the effect that the process variables exert on the microstructure, and, in turn, helps explain the emerging properties. Furthermore, the comprehensive statistical description makes these tools very attractive for the fields of Microstructural Reconstruction and Design.
[1] F. Großwendt, et al., Materials Science and Engineering: A (2021), 827, 142038
[2] C. Cui, et al., Journal of Manufacturing and Materials Processing (2022), 6(4), 72
[3] L. Becker, et al., Materialia, (2022) , 22, 101393
[4] L. Becker, et al., Materialia (2023), 28, 101720
[5] S. Benito, et al., Materials Today Communications (2023), 34, 105016